Centrifugal Compressors: The Basics for Industrial Professionals
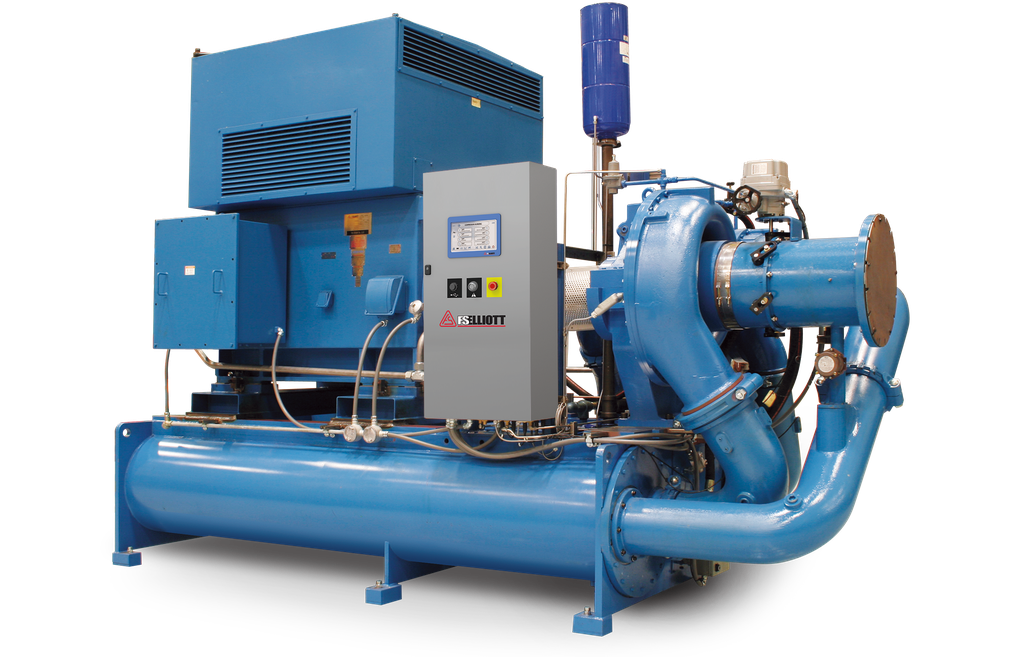
What is a Centrifugal Compressor and How Does it Work?
Centrifugal compressors are an essential component in various industrial applications, known for their efficiency and reliability. But what exactly are centrifugal compressors, and how do they work? This page will explain the key concepts, principles, and applications of centrifugal compressors, helping you understand their importance in your manufacturing operations.
Key Concepts and Principles
Centrifugal Force
At the heart of a centrifugal compressor's operation is the principle of centrifugal force. The compressor uses this force to create a high-velocity flow of gas or air by spinning an impeller within a stationary casing. The impeller's rotation accelerates the gas or air radially outward, increasing its velocity.
Energy Conversion
Energy conversion is another fundamental principle of centrifugal compressors. As the gas or air is accelerated by the impeller, its kinetic energy (energy due to motion) is converted into pressure energy (static energy). This conversion happens in the diffuser section of the compressor, where the high-velocity gas or air is decelerated, resulting in a pressure increase.
Compression Stages
Centrifugal compressors often utilize multiple stages of compression to achieve the desired pressure level. Each stage consists of an impeller and a diffuser, gradually increasing the pressure of the gas or air. The multi-stage approach allows for higher pressure ratios and more efficient compression.
Efficiency and Performance
The overall efficiency and performance of a centrifugal compressor depend on several factors:
- Impeller Design: The shape and size of the impeller blades play a crucial role in determining the compressor's efficiency.
- Speed: Higher rotational speeds can lead to increased efficiency but may also introduce mechanical challenges.
- Gas Properties: The type of gas being compressed affects the compressor's performance. For example, lighter gases like hydrogen require different handling compared to heavier gases like methane.
Applications of Centrifugal Compressors
Centrifugal compressors are used across a wide range of industries, thanks to their versatility and efficiency:
Pharmaceuticals
In the pharmaceutical industry, precision and cleanliness are paramount. Centrifugal compressors are utilized to maintain the purity of compressed air used in manufacturing processes, ensuring that products meet stringent quality standards.
Electronics
The electronics industry relies on centrifugal compressors for cooling and in the production of semiconductors. These compressors provide the necessary airflow to maintain optimal operating conditions for sensitive electronic components.
Automotive
Centrifugal compressors play a significant role in the automotive industry by aiding in the production of various vehicle components. They are essential for tasks such as paint application and powering pneumatic tools, contributing to higher efficiency and quality in manufacturing processes.
Power Generation
In power generation, centrifugal compressors are used in gas turbines and for air separation processes. They help in enhancing the efficiency and reliability of power plants, ensuring a steady supply of electricity.
Utilities
Utilities sector demand high-performance equipment to maintain continuous operations. Centrifugal compressors are employed for water treatment, waste management, and other critical services, providing consistent and dependable performance.
Industrial Manufacturing
Industrial manufacturing encompasses a wide array of processes where centrifugal compressors are indispensable. They are used for material handling, blending operations, and maintaining air pressure in automated systems, ensuring seamless production workflows.
Oil and Gas Refineries
Centrifugal compressors are vital in oil and gas refineries for processes such as gas lift, gas injection, and gas gathering. Their robust design and high efficiency make them suitable for handling the demanding conditions of the oil and gas sector.
Food and Beverage Industry
The food and beverage industry uses centrifugal compressors to maintain hygiene standards and improve product quality. They are utilized in packaging, bottling, and pneumatic conveying systems, ensuring contamination-free processes.
Aggregate
In the aggregate industry, centrifugal compressors power machinery for crushing, screening, and washing aggregates. They provide the necessary air pressure to operate heavy-duty equipment efficiently and reliably.
Aluminum
Aluminum production involves several stages where centrifugal compressors are essential. They are used in the refining process, smelting operations, and in the production of aluminum products, ensuring a continuous supply of compressed air.
Bourbon
In the bourbon industry, centrifugal compressors are used to power pneumatic systems in the distillation process. They ensure smooth operations and maintain the quality of the final product.
Chemical
The chemical industry benefits from centrifugal compressors in various applications, including chemical synthesis, gas processing, and air separation. Their ability to handle different types of gases makes them versatile and highly useful.
Steel
Steel manufacturing requires high-pressure air for processes such as blast furnaces, basic oxygen furnaces, and electric arc furnaces. Centrifugal compressors provide the reliable compressed air needed to produce high-quality steel.
Advantages of Using Centrifugal Compressors
High Efficiency
Centrifugal compressors handle large volumes of gas or air with high efficiency, making them ideal for industrial and commercial applications. Their design allows for continuous operation with minimal energy loss.
Low Maintenance Requirements
Compared to other compressor types, centrifugal compressors have lower maintenance requirements. This leads to reduced operational costs and increased uptime, ensuring reliable performance over time.
High Pressure Ratios
Centrifugal compressors can produce high pressure ratios without the need for intercooling, making them suitable for high-pressure applications.
Superior Reliability
With a longer operational lifespan and robust construction, centrifugal compressors provide superior reliability. They contribute to overall system dependability and reduce the likelihood of unexpected downtime.
Quieter Operation
Centrifugal compressors operate more quietly than other compressor types, making them suitable for noise-sensitive environments such as hospitals and residential areas.
Easy Installation
These compressors are easy to install and require minimal downtime for commissioning. Their straightforward integration ensures a smooth transition in industrial setups.
Enhanced Energy Efficiency
Many centrifugal compressors feature variable speed drive technology, allowing for enhanced energy efficiency. This technology adjusts the compressor's speed based on demand, reducing energy consumption and operational costs.
Conclusion
Centrifugal compressors are indispensable in modern industrial applications, offering high efficiency, low maintenance, and superior reliability. Whether it's for gas turbines or industrial manufacturing, these compressors play a crucial role in various sectors. By understanding the principles and advantages of centrifugal compressors, businesses can make informed decisions about integrating these powerful tools into their operations.
Ready to optimize your industrial processes with centrifugal compressors? Contact our team today at 1-855-GO-ATLAS (462-8527) to learn more about how we can help you achieve greater efficiency and performance.