Atlas' Compresses Air Division Enhances Efficiency for Donaldson Filtration Solutions
When Donaldson Filtration Solutions needed air piping changes at their Frankfort plant, the Atlas Compressed Air Division was there to help!
INSUFFICIENCY IN THE PLANT
Efficiency and productivity are crucial factors in any industrial setting, and maintaining optimal compressed air systems is essential for achieving these goals. Donaldson Filtration Solutions' Frankfort Plant faced significant challenges with their compressed air system due to inefficient piping layouts. Fortunately, Atlas Machine & Supply's Compressed Air Division stepped in to transform the situation, resulting in energy savings and cost reductions.
A PIPING PROBLEM
Over time, as equipment was moved within the Frankfort Plant, the air piping system became convoluted, featuring numerous valves and 90-degree turns. This haphazard arrangement led to a considerable loss of efficiency in the compressed air system. Additionally, the piping was undersized, and the numerous
twists and turns created significant restrictions within the air system. This caused a 10 psi pressure drop from the compressor to the plant header, which necessitated the activation of a second 200-hp Sullair compressor to compensate for the loss.
Before Atlas
After Atlas
ATLAS MACHINE &SUPPLY'S EXPERTISE
Recognizing the urgent need for improvements, Donaldson Filtration Solutions turned to Atlas Machine & Supply's Compressed Air Division to resolve the issues with their compressed air system. Atlas was contracted to rework the piping system from the Compressor to the Air Dryer, the Receiver Tank, and the Plant Header to optimize efficiency.
REPLUMBING FOR EFFICIENCY
Atlas Machine & Supply's team of experts meticulously designed and implemented anew piping layout with appropriately sized components. This systematic overhaul addressed the problems of excessive valves and sharp turns, ensuring a streamlined flow through the system. By replumbing the system with the correct-sized piping, the 10 psi pressure drop was completely eliminated. This crucial change prevented having to cycle on the second 200-hp Sullair air compressor.
PERFORMANCE VALIDATION THROUGH AIR AUDITING
To validate the efficiency gains achieved through the piping changes, Atlas Machine & Supply conducted a comprehensive air audit before and after the modifications. This thorough analysis allowed them to quantify the improvements and demonstrate the tangible benefits of their work.
ENERGY AND COST SAVINGS
The results of Atlas Machine & Supply's intervention at the Donaldson Frankfort Plant proved impressive results. By eliminating the 10 psi pressure drop, and no longer needing to cycle on the second 200-hp Sullair air compressor, this resulted in significant energy savings. In total, the savings amounted to 447,180 kilowatt-hours (kWh) annually, translating to a cost reduction of $40,049 per year.
A TESTAMENT TO EXCELLENCE
The partnership between Atlas Machine & Supply's Compressed Air Division and Donaldson Filtration Solutions' Frankfort Plant serves as a prime example of how addressing inefficiencies in compressed air systems can lead to substantial savings and enhanced productivity. Through a well-executed piping overhaul, the plant eliminated the need to turn on an additional air compressor, resulting in considerable energy and cost savings. This successful project highlights the importance of regularly evaluating and optimizing compressed air systems to maximize their efficiency and minimize operational costs.
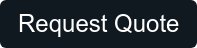