February 24, 2021
Background:
This $200M automotive parts manufacturer located in the Midwest-U.S.A. makes driveshafts that are used for the front-wheel drive, four-wheel drive, and independent suspension systems of rear-wheel drive vehicles.
Driveshafts consist of constant velocity joints (CVJ) and shafts. These items transfer the power of an automobile engine’s rotation to the vehicle’s tires. During a routine inspection of the presses within their facility, the Maintenance Manager of the Forging Dept. noticed what appeared to be some cracks forming in the bed of the press. He knew from experience that these cracks could be considerably worse than meets the eye. After performing ultrasonic testing on the bed, his worst fears became a reality–seven cracks were confirmed
Challenges:
Find a company that can repair the press bed on-site and has the technical knowledge/skills to repair it correctly the first time. Utilize a company that truly understands that “time-is-money” regarding production loss and downtime. They must have a reputation of having technicians with a solution-oriented mindset to get the job done quickly. Ensure that the company selected for the project has the industry reputation and financial strength to stand behind their warranty along with the craftsmanship and quality of services that they provide.
Solution:
Atlas Machine was chosen as the company to solve all of these challenges. Since this automotive parts manufacturer had utilized Atlas Machine’s services since 2010, the Maintenance Manager knew what he would be getting by choosing Atlas. The Atlas On-Site Team immediately went into action by deploying a metrology technician, two welding technicians, and two on-site machinists, at various planned times, to begin the project. Upon arrival, the Atlas metrology technician worked with the customer to measure the press bed and ram to obtain the original datums prior to beginning any repairs.
Once the data collection was complete, the Atlas welding technicians began air arcing the press bed to remove all the cracks found during the original ultrasonic test performed by the customer. As the Atlas welding technicians continued with the process of air arcing the press bed, the cracks were more severe than originally thought. During this process, the Atlas welding technicians discovered 38 cracks instead of seven as originally planned. Once all the cracks were removed, the team welded up the press bed as needed to prepare for machining.
Once the welding process was complete, the two on-site machinists and the metrology technician worked together to set-up the portable milling machine parallel to the press ram. Using the high precision Atlas metrology equipment to set-up the mill ensured the final machining would be as accurate as possible. During the machining process, the Atlas machinist milled the press bed surface to minimize cleanup and also machined out several knock-out bore bushings that were also damaged. In conjunction with the onsite machining process, the Atlas machinists back at our machine shop milled a customer-supplied bolster plate to the required dimensions to maintain the correct press shut height and made several knock-out bushings to freeze and install. Upon completion of the machining process, the Atlas metrology technician went back into action to record and document all the final dimensions for the customer’s review.
Download the full case study below!
Upon final review of the entire repair project and data, the customer’s expectations were exceeded. As a result of Atlas Machine’s craftsmanship, experience, and work ethic, the customer was able to get the press back into production right away. Another satisfied customer is up and running!
Whether it’s on-site milling, turning, boring, or welding…Atlas Machine’s On-Site Machining Team has got you covered.
Give us a call for 24/7 service to speak with one of our on-site machining experts or feel free to click on the button below to complete our Request for Quote Form. We look forward to helping you and your team soon.
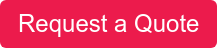